10 min read
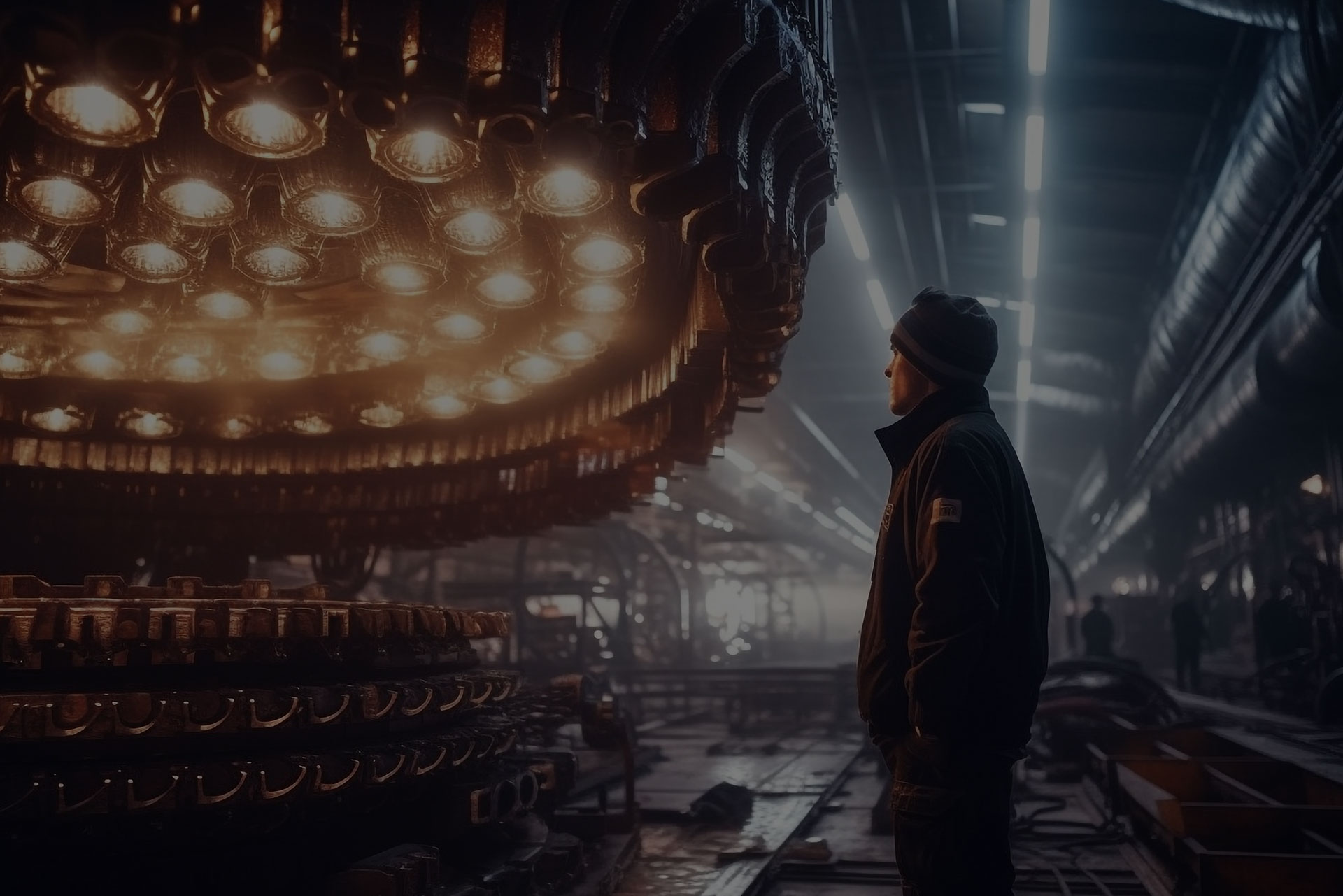
For some time now, the term Industry 4.0 has become very popular, and there is no industry conference nowadays with at least a mention of this topic. The question is, what does it really mean, and what is hidden under this rather capacious slogan? We understand it intuitively – just the next generation of industry, the 4.0 revolution, digitization, the Internet, “everything connected.” However, it’s worth taking a moment to explore the topic, as companies that have not yet embarked on the path of Digital Transformation are said to have little chance of surviving the coming years, as they are incapable of joining modern, automated supply chains.[1] [2]
Why do we even use the term Industry 4.0 or, in other words, the fourth industrial revolution?
History of Industrial Revolutions
The term “industrial revolution” was first used in 1799 by Louis-Guillaume Otto but took on greater meaning in the early 19th century to describe technological changes in industry when the very rapid industrialization of Europe was taking place.
First Industrial Revolution
The beginning of the First Industrial Revolution was when manual labor was replaced by machinery, initially in the textile industry in England. In 1733, the “Flying Shuttle” weaving machine was invented, and in 1764, the “Spinning Jenny” – the first multi-spindle mechanical spinning machine, then improved in 1767 when the manual drive was changed to a water drive (water wheel). At the same time as changes in the production technology itself, changes in the use of coal as an energy source were taking place.
These improvements contributed to the development of James Watt’s steam engine, which could then be used as a source of propulsion for manufacturing. With the increased demand for coal and metallurgical products used to make machinery, industries such as mining, metallurgy, and the iron and steel industry quickly began to develop. During this period, the first steamships (“Clermont,” 1807), the first steam locomotive (Stephenson, 1825), and the first railroads (Stockton – Darlington line, England, 1825) are built.
Second Industrial Revolution
The onset of the Second Industrial Revolution marked a substantial acceleration in technological advancements. During this period, electricity gained widespread use in manufacturing, accompanied by the emergence of innovative inventions. In 1800, Alessandro Volta pioneered the development of galvanic cells, followed by Samuel Morse’s construction of a telegraph apparatus in 1837. The momentum continued with the creation of the first telephone in 1876 and the invention of the inaugural light bulb in 1879. In this era, the inception of automobiles and motorcycles unfolded, accompanied by the invention of various groundbreaking devices such as the camera, typewriter, kerosene lamp, and more. Henry Ford played a pivotal role in industrial progress by introducing the first production line, a transformative innovation that reshaped the landscape of manufacturing enterprises. Establishing the production line is widely regarded as the crowning achievement of the Second Industrial Revolution.
Third Industrial Revolution
The Third Industrial Revolution began in the second half of the 20th century, and its primary marker is the application of programmable electronics to industrial automation. In 1969, the first Programmable Logic Controller (PLC) was developed for the automotive industry in the US (Bedford Associates, model Modicon 084), which opened up entirely new possibilities for industrial process control. Earlier control systems were based on electrical and electronic components that were permanently connected, resulting in very limited reconfigurability. With the use of PLCs, it became possible to “program” machines and production lines, and the design of different systems could now be designed based on the same base hardware, differing only in configuration and software. It is worth mentioning that Modicon 1979 introduced the MODBUS standard for communication between machines and electronic devices.
Fourth Industrial Revolution
We are currently standing on the threshold of the Fourth Industrial Revolution. While it is not entirely sure what it will be, we can already identify its main directions. The most important trend that characterizes the fourth industrial revolution, or “Industry 4.0,” is the interconnection of devices in factories and enterprises into a single, globally accessible industrial network. This is happening mainly due to the development of information technology (IT), which allows the aggregation and processing of large amounts of data from various sources.
Elements of the Fourth Industrial Revolution
It is only possible to discuss Industry 4.0 by introducing key concepts that characterize current trends. While many of them require in-depth discussion, we will focus on listing at least a few of the most important ones; these include:
Industrial Internet of Things (IIoT)
Industrial Internet of Things – this broad term basically boils down to all kinds of sensors and devices connected to the Internet. This allows remote global access to data and process control. Nowadays, the aim is for every device, even the smallest, to be plugged into a worldwide network, reporting on its condition, performance, and possible faults. It is impossible to list all
the advantages of such an approach. However, every automation specialist will appreciate, for example, the ability to send notifications of failures directly to a cell phone (reducing response time to a failure)
DataBus (Data Lake, Data Pool, Message Broker)
Data bus is a concept in which all information related to a given process is “collected” in one place and can be used anytime. The information is aggregated in real-time, taking into account the stability of the connection and the quality of the data, and then used for various purposes – predictive maintenance, Big Data analysis, or Machine Learning and Artificial
Intelligence for production optimization (Golden Batch). In modern Industry 4.0 systems, the role of the DataBus is often played by the so-called Message Broker, the concept of which is implemented in the MQTT protocol.
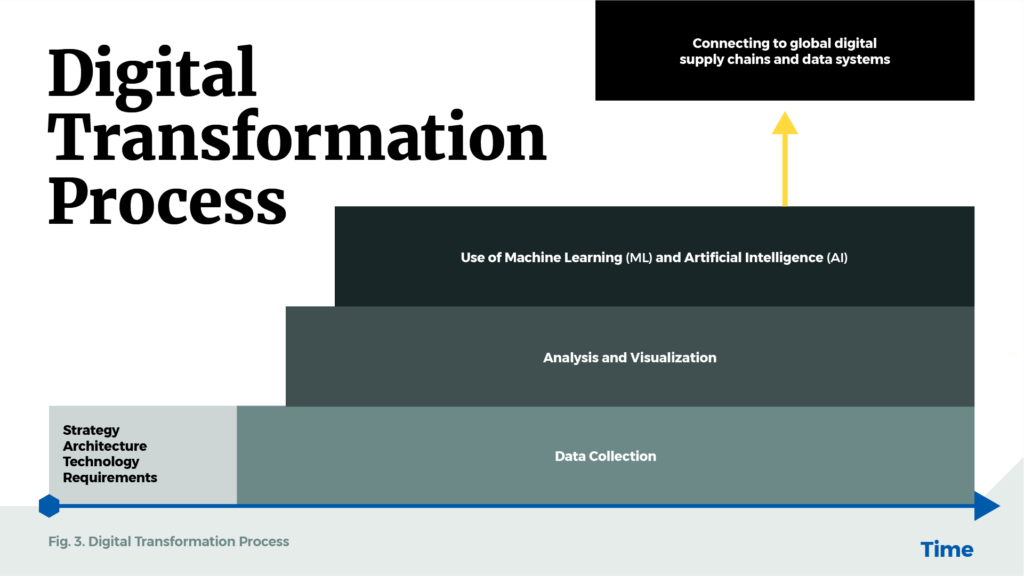
Brownfield and Greenfield
Brownfield and Greenfield are terms distinguishing the nature of the projects at hand. Brownfield projects involve adapting existing facilities to contemporary standards, often requiring integrating various devices from different vendors with distinct communication standards. The focal challenge lies in coordinating these diverse devices, and a critical component in this context is the ‘Edge Device’ or ‘IoT Gateway.’ This Gateway serves as a device facilitating translation and standardization of communication among devices while also establishing a connection to the MQTT DataBus/Broker.
On the other hand, Greenfield projects entail constructing a system from the ground up, providing the opportunity to implement the Industry 4.0 concept from the outset.
Connectors
These are devices or programs that allow us to connect systems, devices, and production lines that do not conform to modern standards to Industry 4.0 systems. They allow us to send data to DataBus/Broker MQTT.
Edge / Edge Device / Edge Computing
Internet of Things devices that provide connectivity to the global network. They typically have some computing power that can be used for data preprocessing (“edge computing”).

Non-Code (Low-Code) programming
Until recently, programming skills were required to program a process control device like a PLC. Despite attempts to standardize PLC programming languages – Structured Text (ST), Function Block Diagram (FBD), Ladder (LD) – programming still required specialized knowledge and experience. Non-Code solutions allow “programming” via a graphical interface, where individual functions, devices, and sensors are assigned appropriate icons. With this solution, no programmer work is required to change the way a particular device or production line works, and it can often be done by people who are well-versed in the process but do not have programming skills.
Digital Twin / Augmented Reality (AR) / Virtual Reality (VR)
Thanks to the use of process virtualization technology, we can reproduce the process more and more accurately in digital form. We are now reaching the point where we can create a virtual model of a particular piece of equipment and simulate the entire industrial process. In addition, thanks to real-time data obtained from DataBus, we can provide virtual simulation data on the fly, making the simulation a perfect representation of the actual process – a Digital Twin.
Digital Transformation and Enterprise Digitization
So, what should you do to modernize your enterprise and reap the benefits of Industry 4.0? Where should you start? How long does the digital transformation process take, and what does it consist of? Finally, why is it even worth doing?
There are many reasons, but the most important are:
- access to automated global supply chains,
- the ability to respond immediately to data obtained from the process,
- more accessible analysis of data sets,
- easier access to information
Thanks to these capabilities, we can optimize the company’s work, better manage resources, or reduce production costs, ultimately improving the company’s overall health.
Pillars of Digital Transformation
The foundation of a successful digital transformation is based on three factors:
- Strategy
- Technology
- Partners
The first step in the transformation from enterprise 3.0 to 4.0 is the right strategy and the understanding that this is not a process of developing legacy technology but a complete paradigm shift in operations[3]. It’s a transformation to an integrated, global, connected system where information can be accessed in real-time and where advanced IT tools can be used. Companies that have undergone digital transformation are referred to as data-oriented or data-driven companies. Adopting the right strategy should allow you to go down this road smoothly without disrupting the existing work of the company. It is very important to be sure that everyone is aligned on the goals we want to achieve and has a clear and consistent understanding of the concepts we use. At this stage, among other things, one determines how technologically advanced an enterprise is by conducting a Digital Maturity Assessment[4].
The choice of technology should be dictated by the strategy adopted. Today, many automation hardware and service providers offer Industry 4.0 solutions, ranging from individual IIoT-compliant devices (Edge Devices) to complete solutions consisting of devices, software, and complete cloud services, including data analysis via Artificial Intelligence.
The right partner should provide a simple, easy-to-understand path to achieve the goal and help estimate costs and time. It should also have experience in similar projects and an in-depth understanding of the processes and requirements of the enterprise to undergo Digital Transformation.
How long does a digital transformation take, and what are the next steps?
Once the strategy and the technology dictated by it are agreed upon, the stage of the actual work at a given facility or plant begins. Keeping in mind that the main idea is to have instant access to data from anywhere, the work starts with data collection and, therefore, connecting devices and sensors to a common “data bus” (DataBus).
All possible sources or recipients of data are considered devices connected to the DataBus, from sensors, production-related machinery and equipment, to logistics systems, data analysis systems, HR systems, production management systems, etc. The process should begin according to the bottom-up technique, starting with connecting the minor elements of the system and grouping them logically, under the structure of the enterprise, into more extensive collections.
The duration of the data collection stage, its standardization, and its connection to DataBus depends on the size of the enterprise and the scope of the project, but on average, it is assumed to last about a year. At the end of this period, the data recipients should be able to analyze and visualize it, which should contribute to a better understanding of the enterprise as a whole of resources and processes occurring in it. What is essential here is that the process of adding new components to our system is continuous and should align with the digital strategy. This means that each new device, sensor, or recipient of information in a given enterprise should be treated as a new component of the Industry 4.0 system.
In the following years, and it is assumed that the entire transformation process may take up to several years, there is an intensive use of computer processing capabilities.
Machine Learning (ML) models are beginning to be used for analysis, which, as a result, makes it possible to predict resource requirements, estimate production costs, and perform predictive maintenance. In addition, thanks to Artificial Intelligence, user interaction with the system becomes easier, and many processes previously performed by humans, such as generating reports or creating orders, are entirely automated. When this happens, joining a global digital automated supply chain is possible, which will help reduce lead times, material costs, and overall labor costs.
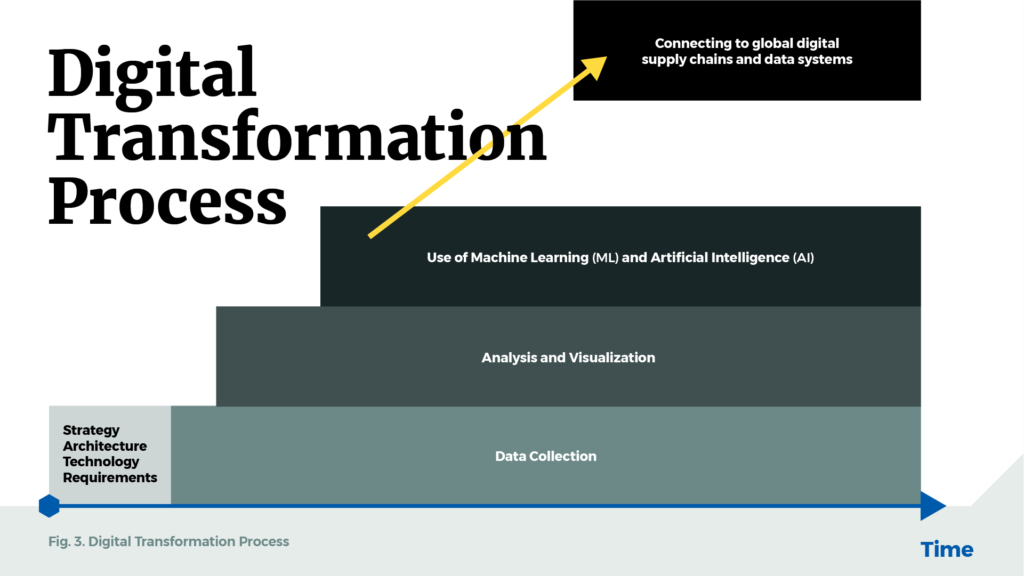
Clearly, the issues presented and the description do not cover the topic completely and the answer to the question of what Industry 4.0 is and what impact it will have on the future of the manufacturing industry is much more complex. Yet it is worth remembering that Digital Transformation is a concept that assumes a change in operating principles from Industry 3.0, based on automated production, to Industry 4.0, which automates business processes through a combination of automation (OT) and information technology (IT) systems.
- “Maintaining competitive conditions in the era of digitalization” OECD report
to G-20 Finance Ministers and Central Bank Governors, July 2018 - “The only way manufacturers can survive” MITSloan Management Review,
2019 - “Survival through Digital Leadership” Deloitte Digital/ Heads! International,
03/2015 - “Mind The Gap: It’s About Digital Maturity, Not Technology” Yilmaz, K. Ö., 2021