5 min read
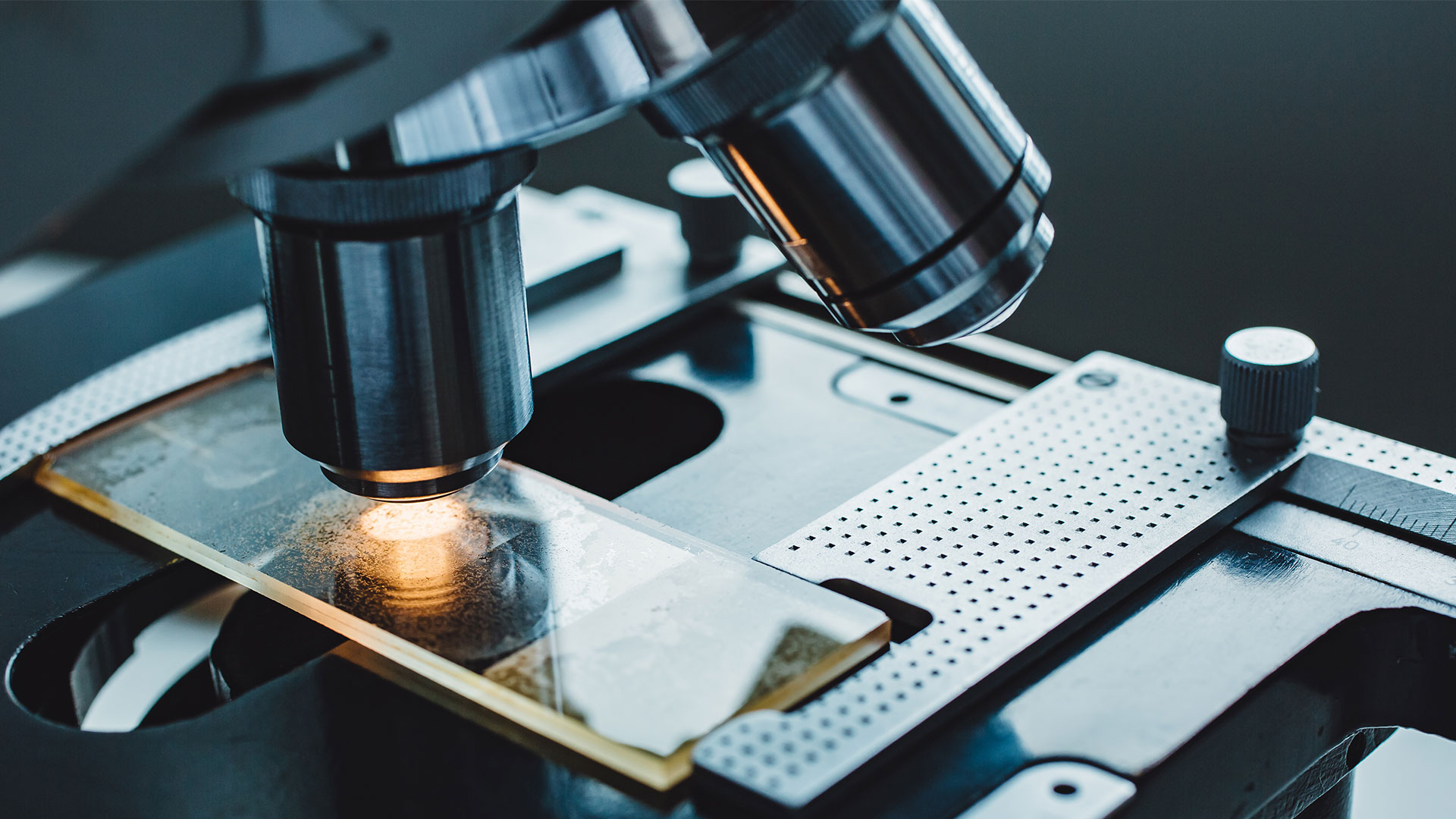
The Covid-19 pandemic has underscored the critical importance of time in the pharma and biotech industries. The dynamic nature of both laboratory and manufacturing operations necessitates swift adaptability in production processes. Surprisingly, these seemingly distinct worlds of laboratories and factories share many common demands from the market, such as the need for rapid response to market requirements, scalability, and short time to market (TTM).
Addressing these demands can be challenging, as hardware and software integration often consumes months and any changes at the production level can lead to costly and time-consuming upgrades. In this article I explore a solution to meet these challenges: modularity, facilitated by Module Type Package (MTP) standardization.
Modular Solutions for Labs and Manufacturing
Imagine delivering a production line or laboratory equipment in the form of modules that clients can configure as needed, wherever they choose. This flexibility can be especially crucial, for example, when setting up a temporary production facility for vaccines, as we witnessed during the COVID-19 pandemic. In situations where just-in-time (JIT) production is required, and demand can fluctuate rapidly, the risk of shutting down a production line or a temporary facility can be eliminated. Modular production line components can be repurposed for other processes, and temporary facilities can be adapted for uses like storage.
Achieving this high level of modularity hinges on standardization, and Module Type Package (MTP) plays a pivotal role in achieving it. MTP allows us to approach each element of a production line or laboratory equipment as a standalone module. By providing MTP files (similar to device drivers) for each module, we gain the ability to recognize the functions of each module from the Process Orchestration Layer.
Efficiency through Standardization
If every device requires nothing more than power and network connectivity, and individual modules can be easily configured through drag and drop in a control application, it becomes evident that minimal engineering effort is required. This vision encapsulates the future of laboratories and manufacturing: a “just plug and produce” approach.
Benefits of Modular MTP Integration
The implementation of MTP and modular approaches offers a range of benefits to both laboratory and manufacturing:
Rapid adaptation
MTP-based modules can be easily added or replaced to accommodate changing requirements swiftly.
Scalability
Expanding or reducing production capacity becomes hassle-free by adding or removing modules.
Cost efficiency
The modular approach reduces the need for costly and time-consuming customizations.
Resource optimization
Modules can be repurposed for various tasks, enhancing resource utilization.
Reduced downtime
Upgrades or maintenance can be performed on individual modules without affecting the entire production line or laboratory.
A Comparison of Traditional Production Setups vs. Modular MTP – Based Setups
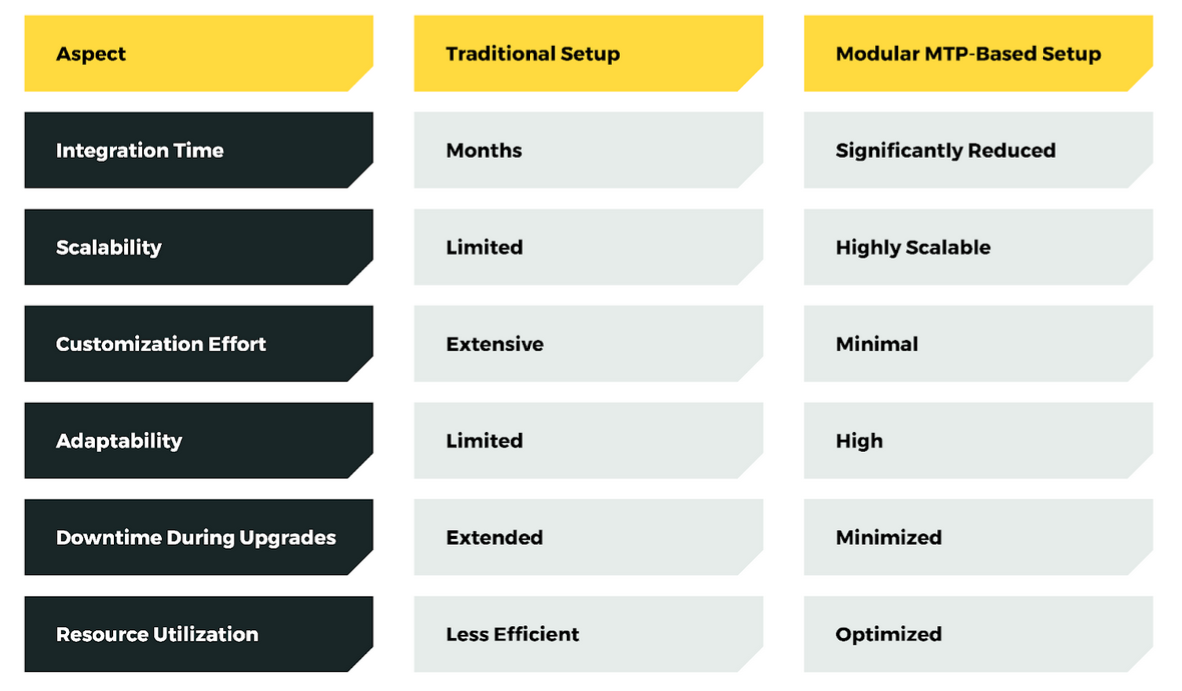
Aspect | Traditional setup | Modular MTP-based setup |
---|---|---|
Integration time | Months | Significantly reduced |
Scalability | Limited | Highly Scalable |
Customization effort | Extensive | Minimal |
Adaptability | Limited | High |
Downtime during upgrades | Extended | Minimized |
Resource utilization | Less Efficient | Optimized |
Conclusion
In the rapidly evolving landscape of pharma and biotech, the ability to adapt quickly is paramount. The integration of Module Type Package (MTP) and modular systems provides the means to meet market demands efficiently, with reduced downtime and resource optimization. As we look to the future, the “just plug and produce” vision promises to transform laboratories and manufacturing, making them more responsive and adaptable than ever before.