Retrofitting legacy chiller with CoreBoard®
Industry
Biotechnology
Scope
Retrofitting / IT / OT / R&D
Timeframe
1 month
-
40h
of development time
-
3000$+
money saved
-
3h
from 40 to 2°C
01
CLIENT
Research unit specialized in biotechnology and life science fields. Takes care of multiple studies such as cell cultures, algae production, organ perfusion, and transplantology.
02
BUSINESS NEEDS
In many biotechnological processes, temperature is a critical factor, both for the environment and the process itself. The need for dynamic temperature regulation is particularly essential, for instance, to maintain optimal conditions for algae growth. But simple regulation is not enough. We need this data to be digitized, stored and must be accessible for other devices to maintain smart processes.
03
CHALLENGE
To help our client achieve its goals, we faced the following challenges:
-
The tank’s contents cannot leave the vessel for temperature regulation.
-
The temperature must be regulated precisely.
-
Rapid and drastic temperature changes may occur.
-
Data must be digitized and available from control application.
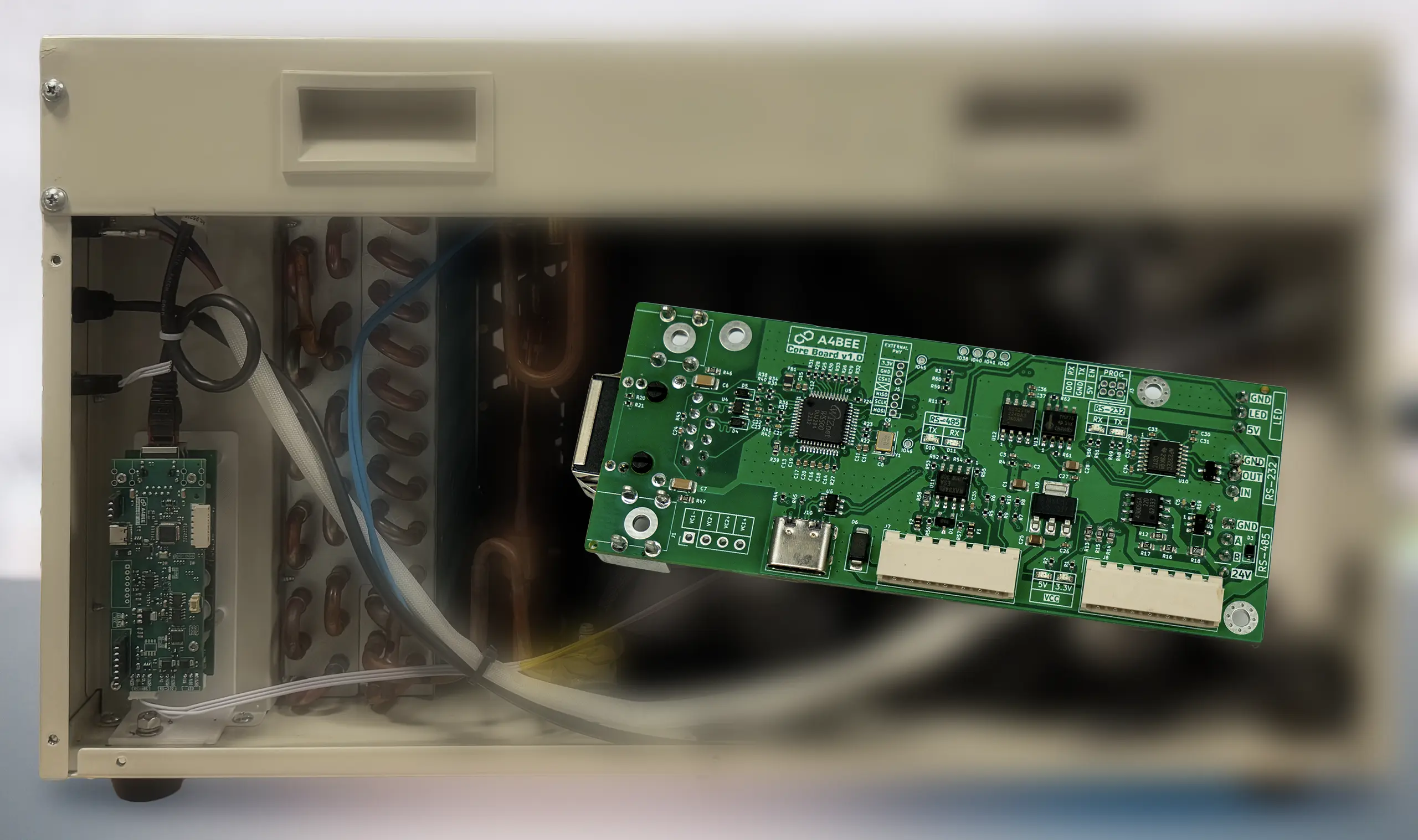
04
SOLUTION
The use of a tank with a water jacket solves the issue of stationary content within the tank.
- Supports various cooling liquids
- Uniform temperature control
- Integrated cooling unit
- Smart orchestration via CoreBoard®
- Dynamic closed-loop regulation
The system allows for the use of different liquids, such as distilled water or glycol, to accommodate specific temperature requirements, including those below 0°C. Flexible and tailored to specific needs!
A regulated liquid surrounds the tank, ensuring even and consistent temperature adjustment. Efficient and precise!
A standard refrigeration unit is used for temperature regulation, offering reliable performance. Simple and effective!
By integrating the chiller with the CoreBoard®, chiller control is possible both through the software and via OPC UA or MQTT, and all information is digitized and transmitted to the system.
With built-in temperature monitoring, the system provides real-time, automated adjustments for optimal temperature management. Adaptive and cutting-edge!
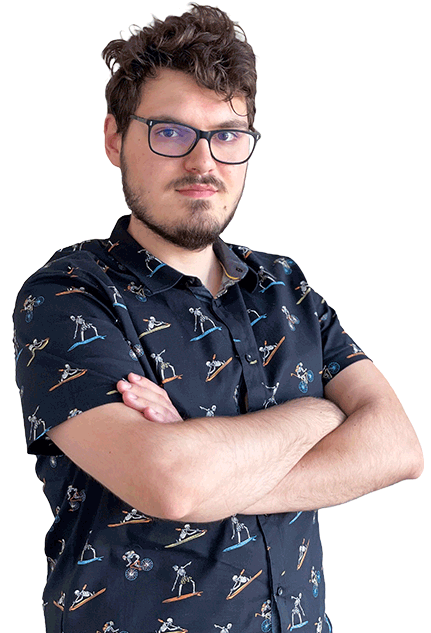
When I first saw the chiller, I thought, “I can’t believe someone is still using equipment like this.” The need to constantly approach the device, check if the temperature was correct, and the inability to gather data was unacceptable. Thanks to CoreBoard® and the amazing team, A4BEE proved that even equipment like this can get a second life and continue to serve effectively. Not to mention the money saved on purchasing a new device and integrating it into the system!
Felix Piątek
R&D Engineer
Technology used
05
OUTCOME
The legacy chiller device has been revitalized with the integration of CoreBoard®, transforming its functionality and extending its usefulness.
- System integration
- Enhanced data handling
- Improved temperature control
- Cost-efficient upgrade
- Powered by CoreBoard®
The chiller can now be controlled directly from within the system, streamlining operations.
It enables the collection and analysis of operational data for better insights.
The system can now regulate based on internal tank temperature instead of just the regulating liquid’s temperature.
This transformation eliminated the need to replace the device with a newer, more expensive model.
A compact yet powerful addition that made all these advancements possible!
-
40h
of development time
-
3000$+
money saved
-
3h
from 40 to 2°C