NextGen Cell Culture Mixing Device: Revolutionizing Biotech Manufacturing
Industry
Biotechnology
Scope
IT/OT
Timeframe
20 months
-
3
total project phases
-
20
months as a total duration
-
30
people in the team
01
CLIENT
The client is a global life science company that specializes in researching, developing, manufacturing, and distributing pharmaceuticals and vaccines. The company focuses on a wide range of health areas, including oncology, infectious diseases, diabetes, and vaccines.
02
BUSINESS NEEDS
Our main task was supporting the software development of a robust, integrated, scalable, and innovative mixing device capable of enhancing operational efficiencies in the biotechnological or pharmaceutical manufacturing processes. We developed IT & OT control software to meet the customer's critical business needs, like implementing a system that seamlessly integrates operational technology components with physical devices. It was extremely important to develop extensive testing protocols and safety features within the system to ensure reliability and compliance with industry standards.
03
CHALLENGE
To help our client achieve its goals, we overcame the following challenges:
-
Integration of existing objects with physical components and their instantiation.
-
Implementation of safety and security logic.
-
Assessment of how many OT objects need to be developed specifically for the project.
-
Preparation of simulation logic in PLC to enable testing of OT components on test Virtual Machines without connecting to physical devices.
-
Designing the system, which prioritizes scalability and efficiency, facilitating future growth and adaptation without requiring significant reinvestments in new technology.
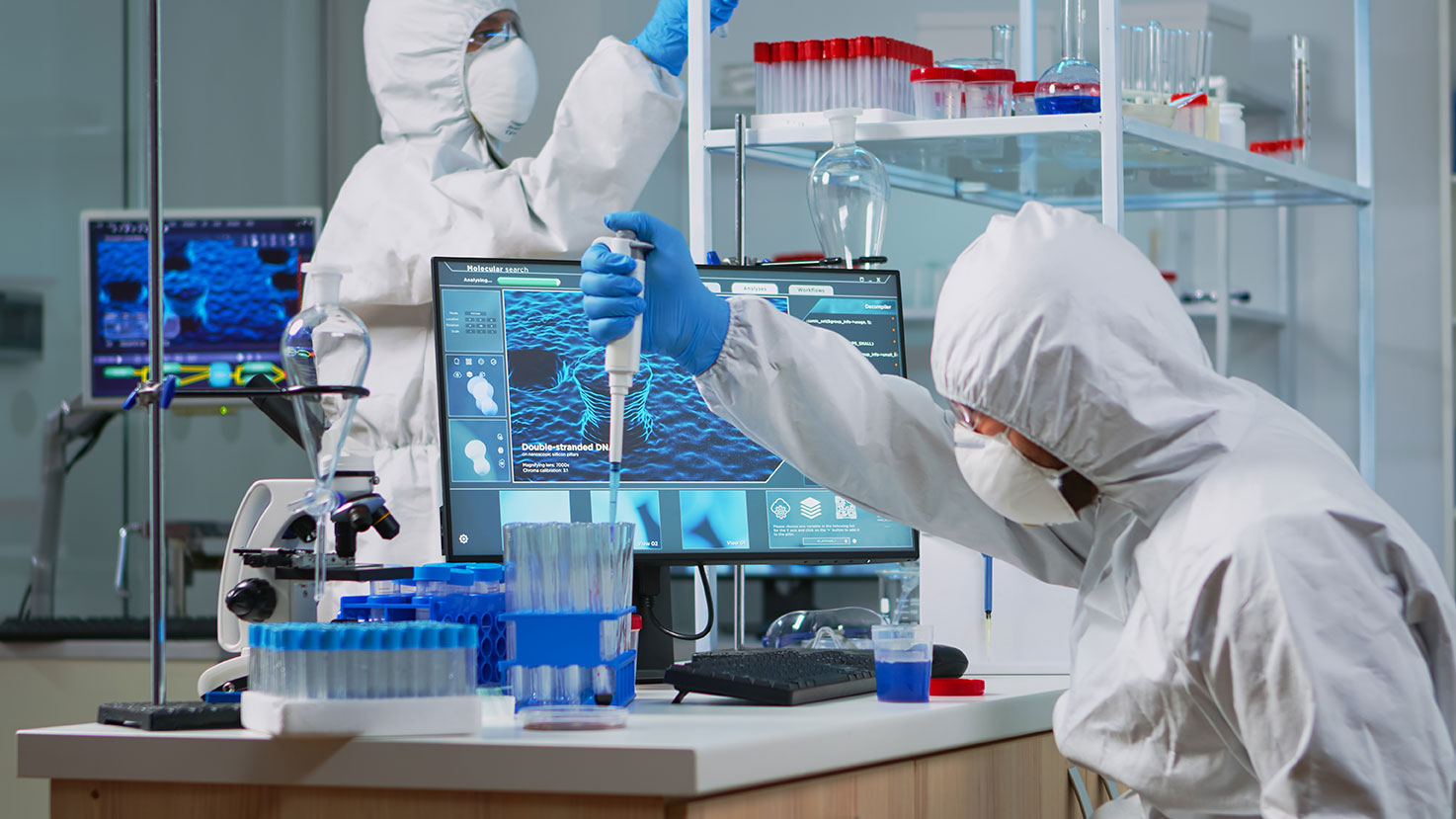
04
SOLUTION
We provided a comprehensive solution for developing the device software, utilizing Agile SAFe methodology for project execution. The solution entailed:
- Manufacturing Process Integration: Making the device versatile enough to be used at any stage of the monoclonal antibodies manufacturing process for storage and buffer/media preparation purposes.
- Integration and Development: Developing and integrating OT components with physical device components such as Control Box, Carrier and Pump Cart, ensuring seamless instantiation and function.
- Testing and Validation: Extensive testing strategies, including simulation tests on virtual PLCs and physical PLCs to ensure the software and hardware components work flawlessly together without connecting to physical devices initially.
- Device Functionality: Creating a device software, supporting blending and homogenizing different types of powders and liquids to produce a homogeneous solution.
- Biotech Applications: Ensuring the device is suitable for media preparation, feed preparation, refolding, viral inactivation, antibody drug conjugation, and as a storage tank.
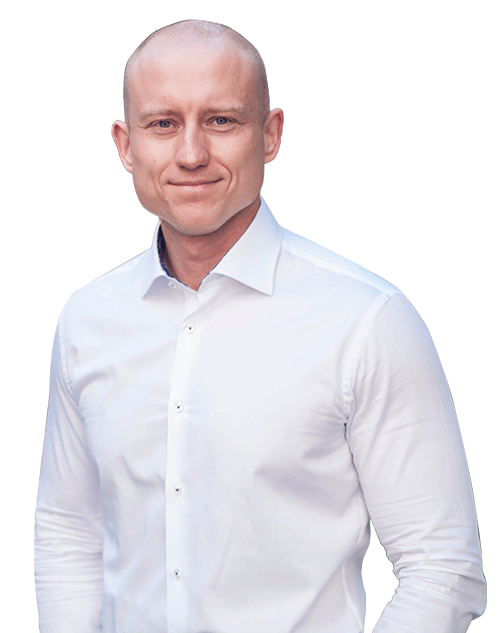
This project required a seamless integration of cutting-edge technology with robust project management practices. From a project management perspective, the key to success was maintaining transparent and continuous communication with customer teams, ensuring all stakeholders were aligned. We also focused on cultivating strong teamwork and adaptability among A4BEE and the client's project members to meet evolving project demands. Integrating Operational Technology (OT) with physical systems while ensuring safety and compliance with industry standards demanded technical proficiency and a high level of coordination and problem-solving capabilities. Ultimately, it was A4BEE's commitment to these principles that guided the project towards meeting its strategic objectives.
Piotr Buchart
Delivery Executive
Technology used
05
OUTCOME
We developed a scalable, reliable system based on the client's existing frameworks and technology stack, enhancing productivity and flexibility in monoclonal antibody manufacturing. The solution supports seamless expansion with customizable pumps, sensors, and filters, all while maintaining high safety and performance standards. The device integrated advanced software solutions with physical components effectively. We emphasized safety and security within the development process, ensuring that the system adheres to high standards of operational safety and performance.
- Integrates advanced software solutions with physical components effectively
- It can be used across various stages of the monoclonal antibodies manufacturing process enhanced flexibility and productivity
- Adheres to high standards of operational safety and performance - we emphasized safety and security within the development process
- Makes the device effectively manageable and scalable, leveraging both A4BEE's technology solutions and existing customer frameworks
06
IMPLEMENTED SOLUTION
- support of temperature, weight sensors, modbus conductivity, ph sensors
- handling agitator, virtual volume and differential pressure sensors
- handling four external pumps
- managing three types of pump cart with pumps
- additional flow and pressure sensors in pump cart support
- control of external analogue and digital inputs and outputs
- control loops controlled by various sensors with many schemas
- external temperature unit to cooling and heating fluid in carrier
- IT services: trends, analytics, alarm, recipes, reports, users and backup
- customizing switchable configuration for Smart Mixer
- OPC-UA Connectivity
- managing settings between OT and IT
-
3
total project phases
-
20
months as a total duration
-
30
people in the team